Embracing 3D Modelling & Printing Technology to Design a Complex Bespoke Ring
- Becca Williams
- Dec 11, 2023
- 3 min read
If you walk into my jewellery studio in Cornwall, you’ll see I’m surrounded by tools of my trade. There are saw blades, blowtorches, jewellers files, clamps, hammers and more, the artisan skill of making jewellery is often largely physical, and uses traditional processes.
Not to make myself sound like a stickler for the ‘old ways’ though, my studio also has machinery and equipment which makes my process more efficient.

In recent years I’ve also embraced new technology, in particular 3D printing which is a brilliant way to offer a physical manifestation of designs during their development stage. 3D printing is great for more intricate, challenging jewellery, as it’s incredibly precise. This can be really helpful for clients to see tangible, early versions of their complex bespoke pieces, before they're fully realised.
Although my traditional techniques are the backbone of my practice, I’m always fascinated by the possibilities of jewellery design and what new processes can bring to the table. Honouring artisan jewellery techniques while embracing new technology can improve designs, and really helps with my collaborative approach.
Bespoke Sapphire and Diamond Ring - Made in Cornwall
A’s Custom Jewellery Brief
The lovely ‘A’ came to me with her engagement ring and eternity rings, which were all beautiful but no longer suited her lifestyle. She hoped they could be remodelled into one stunning ring that she’d be able to wear everyday.
This meant the settings would have to be sturdy and low level, so the stones were secure and wouldn’t catch. Talking of stones, there were plenty! Which meant the real challenge was arranging them all in just one spectacular ring.

Digital Drawing
Having spoken with A and narrowed down general design options, I began to work on the specifics of the ring, where each gemstone would go and how these settings could sit together in a harmonious way.
By drawing digitally, I could continuously play with the options, juggling gemstones until I reached placements which worked, and looked beautiful. How satisfying is the little drawing video below which shows my progress?
3D Printing Rings
Next came the high tech fun part! A 3D model was made of the ring, and two versions were printed in resin for A to try on. With such an intricate and large ring, it was important A could get a proper feel of how it would sit on her finger, and whether it felt comfortable and secure enough to wear daily.
Dismantling Sentimental Jewellery
With a happy client and the design finalised I excitedly began the process of remodelling A’s sentimental rings. The first step was to carefully dismantle her existing engagement and eternity rings. One large sapphire and lots of diamonds - the stones were all removed to leave me with the 18ct gold, ready to be melted.
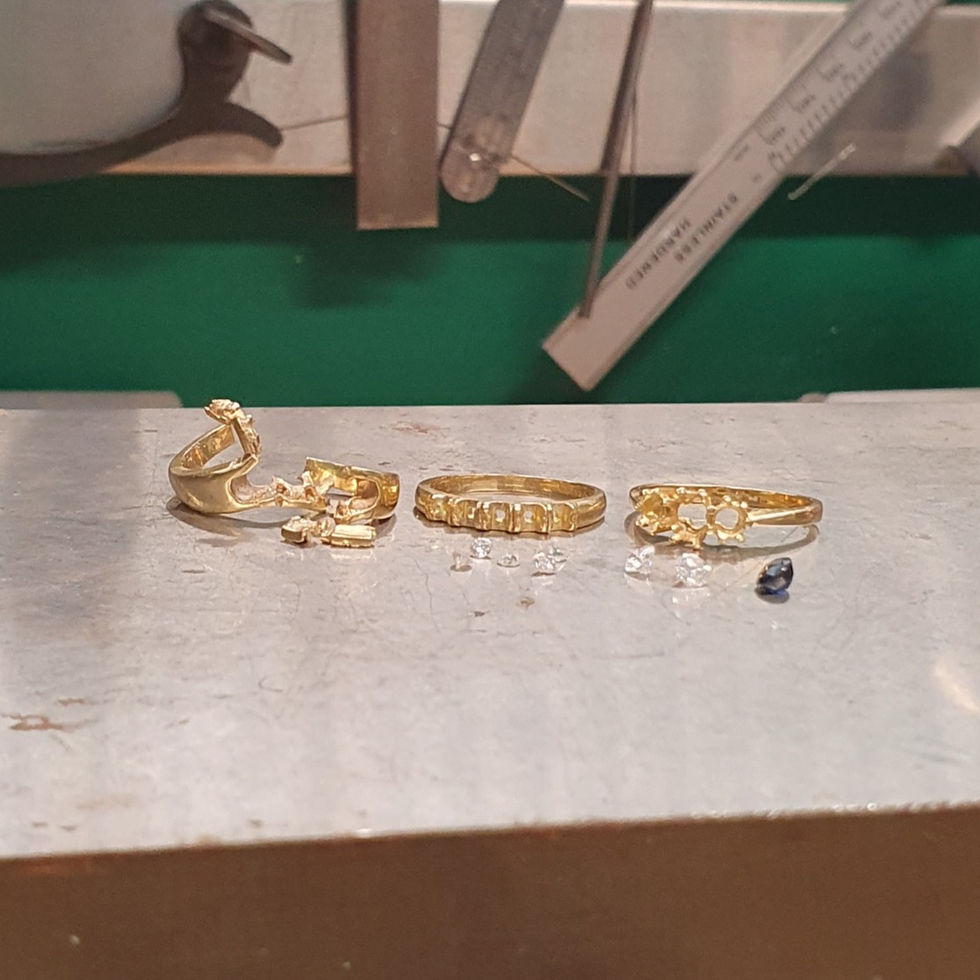
Melting Existing Metals
The gold rings were then melted down, to combine the three separate pieces into one ingot of gold which would be used to create the new ring.
Casting the New Ring & Inserting Stones
The complex new ring was cast from the melted metal, ready for the sapphire and diamonds to be set. The result is just so stunning! The sapphire and two smaller stones next to it are the stones from A's original engagement ring, these stones and story are central to this new design and remind A of that very special ring and all the memories it held.
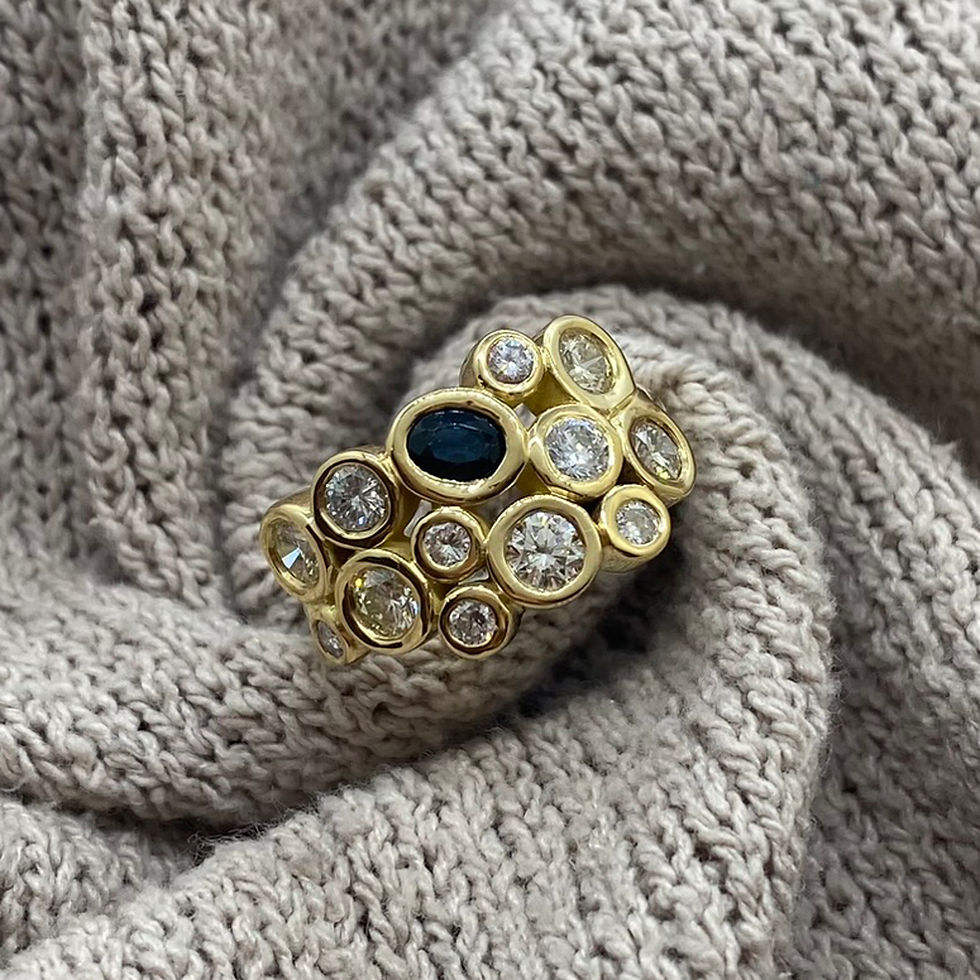
Have you been inspired to start your own bespoke jewellery journey in Cornwall?
As a trained goldsmith with over 15 years experience, the traditional techniques of luxury jewellery making are second nature to me now. I recognise the value in the new and the old (which feels like an appropriate metaphor for remodelling!) and I love to use new technology to open up a world of possibilities, and bring you, the client, into a collaborative, exciting commission.
You can book a relaxed, no-obligation chat with me via the contact form at the bottom of the page. Or click below to find out more about how the commission process works.
Commentaires